
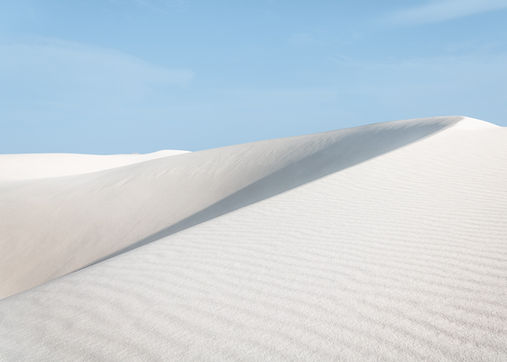
Digital Maker & Fabrication (DMF) Program Objectives
SIP411 Boards Walkthrough
You can view the video on Vimeo below:
Objective 1: Using digital and physical tools, engineer and build prototypes that technology patents are then applied for.
NextGen "Kick"stand
The NextGen "Kick"stand is a lightweight 3D printed kickstand alternative for a bicycle. In this project, I utilized CATIA for this project to create the digital model. This process involved carefully considering the design's structural integrity and usability, ensuring that it would be both functional and aesthetically pleasing. Once I was satisfied with the digital design, I proceeded to the physical realization of the prototype using a 3D printer - specifically the Ender 3 Pro. This allowed me to translate my digital design into a tangible, functional kickstand alternative, showcasing the seamless integration of digital design and physical manufacturing in prototype development.
"Retro" Business Card Box
I designed and built a business card holder box, perfectly aligning with the course objective of utilizing both digital and physical tools for engineering and building prototypes. I used Autodesk Inventor for the digital design, creating a detailed and functional model that included a main hinge pin and a complex latching mechanism with an auxiliary latch hinge pin. This process not only showcased my proficiency in digital design but also my understanding of mechanical principles. Following the design phase, I transformed this digital model into a physical prototype, demonstrating my ability to bridge the gap between virtual design and tangible creation, a key skill in modern engineering and prototyping.
Objective 2: Build physical products while demonstrating technique and safety competency across commonly accepted prototyping devices, maker tools, and techniques.
Fusion Simulation: NextGen "Kick"stand
I modeled the project in CATIA, showcasing my ability to utilize 3D modeling software. Then, importing the model into Fusion360 for static force simulations demonstrates my competency in employing multiple software platforms for comprehensive product development.
By running static force simulations with varying amounts of force, I effectively tested the durability of the material. This not only shows my understanding of material properties and stress analysis but also reflects a methodical approach to ensuring product safety and real-world viability.
The actual 3D printing of the kickstand highlights my hands-on skills with modern prototyping devices. My focus on creating a lightweight yet durable product exemplifies an innovative approach to design, balancing practicality with material efficiency.
Custom Bicycle Stem Cap
Initially modeling the stem cap in CATIA allowed me to apply detailed design skills. Further customizing the model for 3D printing shows my ability to adapt designs for specific manufacturing processes.
Opting for resin 3D printing for this project indicates my proficiency in selecting appropriate manufacturing methods. Resin printing requires a thorough understanding of the printing process, material properties, and safety measures due to the nature of the resins used.
Customizing the stem cap also demonstrates my ability to not only consider the functional aspects of product design but also the aesthetic and user-experience elements, which are crucial in modern product development.
Objective 3: Produce products that balance form and function while reflecting current and future trends in design and human factors.
"Retro" Business Card Box
In my business card holder project, I successfully met the objective of producing products that balance form and function while reflecting current and future trends in design and human factors. Utilizing Autodesk Inventor for digital design and creating a physical prototype, I showcased the essential modern engineering skill of merging digital conceptualization with tangible creation. This approach is increasingly important in contemporary design practices, where digital tools are integral to the initial design phases.
The business card holder was crafted to be not only functional but also aesthetically pleasing. Its complex latching mechanism and hinge pin were designed to be both practical and visually appealing, mirroring the current trend of integrating efficiency with aesthetic appeal in product design. The innovative nature of the latching mechanism, coupled with a keen consideration of human factors like usability and ergonomics, highlights a forward-thinking design approach. It demonstrates an alignment with current trends that favor products which are not just technically sophisticated but also user-centric.
The design's practical application of mechanical principles underlines the product's reliability and functionality. This focus is in line with contemporary design trends that value dependable and innovative products. Through this project, I demonstrated a blend of technical expertise, aesthetic sensitivity, and user-focused design, reflecting the evolving demands and trends in the field of product design and development.
Custom Bicycle Stem Cap
In my stem cap design project, I balanced form and function, aligning with the objective of producing products that reflect current and future trends in design and human factors. The cap's primary role in securing the bike's headset and steerer tube was meticulously addressed, ensuring structural integrity and safety. Going beyond mere functionality, I infused aesthetic appeal into the design, transforming the cap into a statement piece that resonates with the growing consumer preference for personalized and customized products. My design incorporated elements like minimalist lines and unique textures, aligning with current design trends and elevating the cap from a simple component to a modern bicycle accessory.
Furthermore, I considered user interaction extensively, focusing on ease of installation and ergonomic factors, demonstrating a forward-thinking approach in design. This project exemplifies my ability to create products that are not only functional and aesthetically pleasing but also relevant and responsive to evolving trends and user needs, embodying a combination of form, function, and foresight in design.
Objective 4: Demonstrate the ability to evaluate material and build technique options during the creation of products and their prototypes. Demonstrate the ability to effectively implement embedded systems and fundamental electronics into product builds.
Fusion Simulation: NextGen "Kick"stand
In this project, I demonstrated the ability to evaluate material and build technique options during the creation of products and their prototypes, aligning with key objectives of my program. My comprehensive analysis of material properties for the kickstand involved assessing factors like strength, flexibility, weight, and durability. This careful consideration ensured the selection of a material that would excel in real-world cycling conditions, factoring in environmental exposure, wear and tear, and load-bearing capacity. Utilizing Fusion360, I conducted simulations applying varying forces to test the material's resilience, crucial for understanding its performance under actual use. This step illustrated my methodical approach to material testing and prototype development.
Moreover, I adapted the design based on simulation outcomes, showcasing an iterative process in refining the prototype for functionality and reliability. Opting for 3D printing as the manufacturing method, I displayed a deep understanding of its intricacies, making informed decisions about print orientation, layer height, and infill patterns to optimize the strength and weight of the final product. The design was tailored specifically for 3D printing, considering aspects like overhangs and support structures. Throughout the project, I adhered to safety standards pertinent to both product design and the 3D printing process, underlining my commitment to user and operational safety.
Housing for my RES SIP
(Nicotine Rugpull)
In the CATIA design process, I focused on creating a housing that was optimized for 3D printing as the production method. This required a deep understanding of this manufacturing techniques, especially in aspects like ensuring the structural integrity, precision in dimensions, and ease of assembly of the final product. The prototyping phase involved iterative adjustments to perfect the design for efficient manufacturing.
The design of the housing took into account the operational stresses it would encounter. This included ensuring the housing could securely contain and protect the internal electronic components while remaining user-friendly and durable in everyday use.
The challenge lay in integrating dual coils, a battery, control circuitry, and other electronic components into a compact housing. My design ensured there was adequate space for each component while maintaining the device's overall compactness and ergonomic design. This involved a careful balance of spatial planning and component layout to optimize functionality and user handling.
Developing and coding the software for the device was a key aspect. The software controlled various functions like battery management and user interface interactions. This integration of software with the hardware components showcased my ability to create a cohesive system where both physical and digital elements worked in harmony.
The design includes a user-friendly interface, which is essential for the device's purpose as a nicotine cessation tool. This meant creating a gamified interface that was fun, intuitive, easy to navigate, and provided clear feedback to the user. The interface design also had to be seamlessly integrated into the housing, maintaining aesthetics and ergonomic usability.
The Embedded Systems portion of this project can be found on the RES page.
Objective 5: Demonstrate proficiency with industry accepted prototyping, modeling, build and maker tools and techniques.
3D Animal Cell Model
In this project, I ventured beyond my comfort zone with CATIA and SolidWorks to embrace Tinkercad, showcasing my adaptability and eagerness to learn in the dynamic field of 3D modeling and fabrication. This transition not only highlighted my ability to navigate different software complexities but also underlined my proficiency in conceptualizing and designing intricate structures. The project entailed transforming the complex biology of an animal cell into a detailed 3D model, demonstrating my capability to simplify sophisticated concepts for greater clarity. My background in 3D design enhanced my approach to Tinkercad, allowing me to apply sophisticated design principles within a more straightforward platform. This project was a practical application of theoretical knowledge, bridging the gap between conceptual understanding and tangible modeling, a vital competency in the realm of 3D modeling and fabrication. Through this, I illustrated a comprehensive grasp of industry-accepted prototyping, modeling, and fabrication techniques.
Fusion Simulation: NextGen "Kick"stand
In this project, I effectively demonstrated my proficiency with industry-accepted prototyping, modeling, build, and maker tools and techniques. Initially, I modeled the project in CATIA, leveraging my skills in advanced 3D modeling software. This step showcased my ability to create complex designs and prepared the groundwork for further analysis. I then imported the model into Fusion360, which highlights my competence in utilizing multiple software platforms for a comprehensive approach to product development. This integration of different tools is often crucial in modern engineering and design workflows.
Running static force simulations in Fusion360 allowed me to test the durability of the material under various forces, showcasing my understanding of material properties and stress analysis. This process is fundamental in ensuring product safety and viability in real-world scenarios. Furthermore, the actual 3D printing of the kickstand emphasized my hands-on experience with modern prototyping technologies. My focus on developing a lightweight yet durable product exemplified an innovative approach to design, balancing practicality with material efficiency. Throughout this project, I demonstrated a strong grasp of the technical skills and methodologies required in today's prototyping and fabrication industry, aligning perfectly with the objective of my degree program.
Objective 6: Place prototypes and builds within the Agile and MVP development frameworks.
"Retro" Business Card Box
In my Business Card Holder project, I employed the Agile and Minimum Viable Product (MVP) frameworks to guide the development process. Starting with a basic prototype, I embraced Agile's iterative approach, quickly identifying and rectifying design flaws like hinge placement and wall thickness. This cycle of rapid prototyping, testing, and refining is fundamental to Agile methodology. Each iteration served as a functional MVP, starting from the most basic design and evolving based on real-world feedback and practical testing. This process exemplified the MVP philosophy of focusing on essential features and continuously enhancing the product based on user interaction.
Furthermore, I tackled practical challenges such as design tolerances, reflecting the real-world application crucial to both Agile and MVP. This hands-on experience was invaluable in understanding the importance of design flexibility and adapting to imperfections. My project's evolution also highlighted a user-centric approach, prioritizing usability and durability, core to the MVP concept. Through this project, I demonstrated not just my 3D modeling and fabrication skills, but also a deep comprehension of Agile and MVP methodologies, essential in modern product development.
NextGen "Kick"stand
In this project, I applied the Agile and Minimum Viable Product (MVP) development frameworks effectively. The project began with a fundamental design that focused on key functionalities, aligning with the MVP approach of creating a simple yet functional product. Iterations were made based on testing and practical feedback, demonstrating the Agile methodology's emphasis on continuous improvement and adaptability. For example, adjustments to the kickstand's angle and stability were made after initial testing, reflecting the iterative process typical of Agile development. These modifications not only improved the product's usability but also showcased my ability to rapidly prototype, test, and refine the design based on real-world application and user feedback.
The project's evolution from a basic prototype to a more refined and functional product exemplified the MVP concept. By concentrating on essential features and gradually enhancing them through successive iterations, I ensured that the kickstand was both practical and user-centric. This approach underlined my understanding of prioritizing customer needs and functionality in product development. Overall, through the Kickstand project, I demonstrated my proficiency in applying Agile and MVP frameworks, crucial for modern prototyping and fabrication processes.